When it comes to exploring the solar system, rockets dominate the headlines. However, one of the most important aspects of space exploration is more mundane: regolith, a disaggregated mix of dirt and rock that can be found on the moon, Mars, asteroids, comets, and even on Earth. The inorganic mixture can contain valuable minerals and its byproducts can be used to support both on-site colonies and communities on Earth. The challenge is finding a way to mine bulk materials in a low- or zero-gravity environment.
Read this case study to learn about:
- How compact, commercial off the shelf (COTS), high power-density servo drives enable robot navigation in low-gravity, rugged environments
- Advantages of getting top servo performance, advanced networking and reliability, all in a small, PCB mountable package
- Minimizing your development time, resulting in short time-to-market
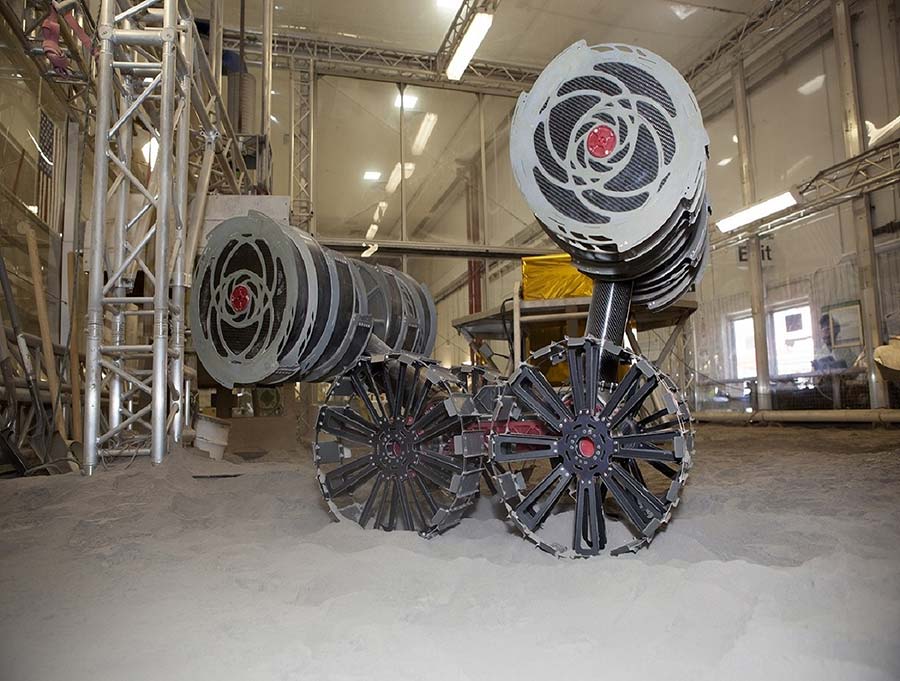
Figure 1: RASSOR uses opposing rotating drums to create a net-zero-force excavator for collecting surface material from objects such as the moon, Mars, and asteroids. (Courtesy of NASA)
Machine requirements
Enter the Regolith Advanced Surface Systems Operations Robot (RASSOR), a teleoperated mobile robot developed by NASA to mine and transport regolith in low- or zero-gravity environments. Designed for proof of concept, the RASSOR was to be built using primarily rugged, commercial off-the-shelf (COTS) components that minimize size, weight, and power consumption. Andrew J. Nick, a robotics engineer at Bionetics (a NASA contractor) says: “We strive to find commercial products that meet our demanding weight and space constraints, and that have the ability to read multiple sensors in a package where we don’t have to do a lot of research and development. We can just use the products and focus on the research.”
RASSOR is based on a pair of counterrotating bucket drums mounted on a mobile robotic platform. Each bucket drum is independently powered by a servo axis and mounted on an independently controllable robot arm with a single rotary axis mounted on a wheeled mobile robotic platform. The combination of the bucket drum rotation and the robot arm positioning enables RASSOR to perform acrobatics for advanced positioning and evading obstacles.
Balancing the forces of the counterrotating bucket drums involves high-resolution feedback and complex digging algorithms. Its complex motion requires the joints to switch between operating modes, for example velocity and position, as well as receive feedback to allow the joints to operate in coordination.
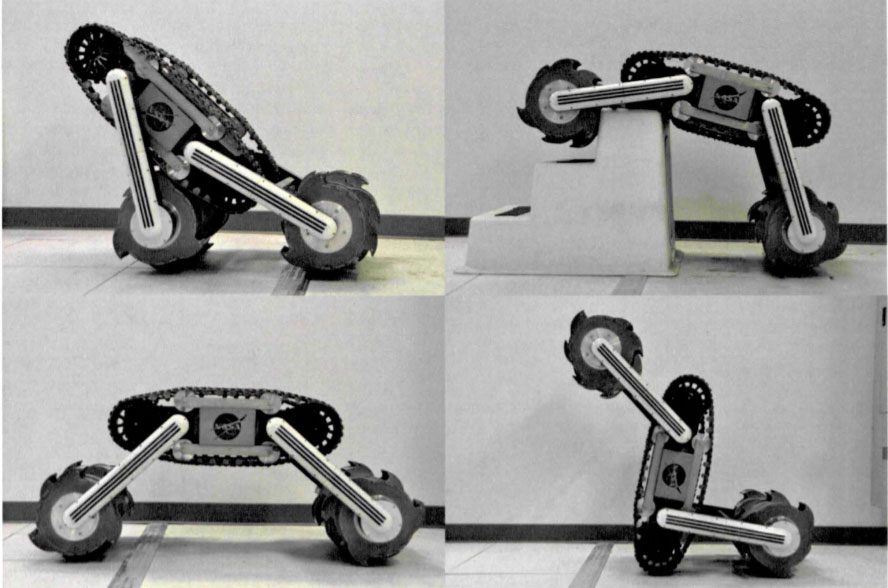
Figure 2: The combination of the rotating arms and bucket drums enables an early version of the RASSOR to (clockwise from top left) flip itself over, climb obstacles, assume a Z position to empty drums into oversized hoppers, and raise the wheels off the ground in order to escape a surface trap or remove debris. (Courtesy of NASA)
Motion Control Solution
- Gold Solo Whistle drive
The excavator incorporates a total of 10 motion axes: two motors for each drum, two motors for each arm, and a pair of motors to drive the wheels of the chassis. It uses a combination of absolute optical encoders on the load and incremental optical encoders on the motor shaft.
Given the level of complexity and the amount of feedback involved, NASA needed intelligence at the drive level. “RASSOR is not just a dumb ‘driver-in-the-loop’ robot,” said Nick. “We needed more than basic drives turning motors off and on. We needed smart motors with feedback and controls.”
The team chose Gold Solo Whistle drives from Elmo Motion Control to meet their needs. Each drive can operate in current mode, velocity mode, and position mode. The PC controller sends basic motion requirements over CANopen. The drives self-manage commutation, current regulation, velocity regulation, and position loops. The drive’s internal trajectory generator uses target end points with acceleration/deceleration and speed information to plan the path and position the load.
The drives offer extremely high-power density, making them a good fit for the space-constrained RASSOR. They are also qualified for industrial applications and rugged enough to tolerate the high shock and vibration of the application. Conformal coatings also help protect against fine dust that might penetrate the enclosure. The team used Elmo Application Studio, Elmo’s drive tuning and configuration software, to fine tune bouncing and other disturbances.
Today’s Solution:
Elmo has introduced new solutions and options since this robot was designed. Today:
- The system can be controlled and operated using Elmo’s Platinum Maestro (PMAS) motion controller, through a wireless network from a centralized PLC or computer.
- The application can utilize the Gold Solo Twitter servo drive.
- Elmo’s unique “R” type servo drive would provide higher continuous current capabilities – ideal for high-inertia motion systems (such as AGVs) that may need high current for extended periods to overcome obstacles.
Gold Solo Twitter
NANO Servo Drive Up to 5600 Watts
Up to 30A/60V, 25A/100V, 10A/200V
Up to R50A/60V, R80A/80V, R70A/100V, R45A/150V, R35A/200V